Understanding the Differences: Direct Thermal Labels vs. Thermal Transfer Labels
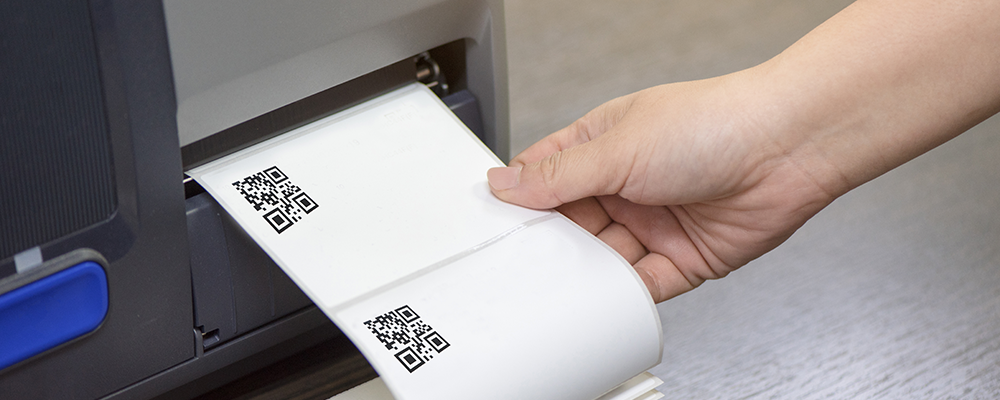

Labels do a lot of heavy lifting across different industries—from keeping inventory organized to making sure shipments get where they need to go. Choosing the right label type can help you work faster, cut down on mistakes, and save money along the way.
Two of the most common options out there are direct thermal and thermal transfer labels. Each has its own strengths, and the best pick depends on how you’re using them.
In this guide, we’ll break down how both types work, when to use them, and what to keep in mind when deciding which one is right for your business.
What are Direct Thermal Labels?
Direct thermal labels are made from heat-sensitive material that darkens when exposed to a thermal printhead—no ink, toner, or ribbons needed. They're a simple, cost-effective choice for businesses that need fast, reliable label printing.
How They Work
Instead of using ink, direct thermal printers apply heat to the label surface, which reacts to create the image. It’s a clean, efficient process that’s great for short-term uses like shipping, receipts, or barcode labels—especially when you're printing in high volumes.
Advantages of Direct Thermal Labels
There are several advantages to using direct thermal labels:
- Cost-Effective: Direct thermal printing eliminates the need for ribbons, ink, or toner, reducing ongoing costs.
- Ease of Setup: The printing process is simple, requiring fewer components and less maintenance.
- Quick and Efficient: Ideal for high-volume printing where speed is essential.
- Best for Short-Term Use: Perfect for applications where labels are not exposed to harsh conditions or need to last for a limited period.
Disadvantages of Direct Thermal Labels
Despite their benefits, direct thermal labels also have some limitations:
- Susceptibility to Environmental Factors: The labels can fade or darken when exposed to heat, light, or friction.
- Limited Longevity: They are not suitable for long-term use as the print can degrade over time.
- Not Ideal for Harsh Environments: Direct thermal labels are best used in controlled environments where they are not exposed to elements that can affect their readability.
What are Thermal Transfer Labels?
Thermal transfer labels use heat and a ribbon to create durable, long-lasting prints. The ribbon is coated with wax, resin, or a mix of both, and the heat from the printer melts that coating onto the label surface.
How They Work
As the label and ribbon move under the printhead, heat transfers the ink from the ribbon onto the label. This method produces crisp, long-lasting prints that hold up well in tough environments—perfect for labels that need to last through heat, moisture, or heavy handling.
Advantages of Thermal Transfer Labels
Thermal transfer labels offer several key advantages:
- Durability: The prints are resistant to fading, heat, moisture, and chemicals, making them ideal for long-term use.
- Versatility: Suitable for a wide range of materials, including paper, polyester, and polypropylene.
- High-Quality Prints: The method produces sharp, high-quality images and text.
- Best for Harsh Environments: Perfect for applications where labels need to withstand exposure to various damaging factors.
Disadvantages of Thermal Transfer Labels
However, thermal transfer labels also have some drawbacks:
- Higher Initial Cost: The need for ribbons and more complex equipment increases the initial setup cost.
- Complex Setup: The printing process involves more components, requiring careful setup and maintenance.
- Ongoing Costs: Regular replacement of ribbons adds to the ongoing operational costs.
Applications of Direct Thermal vs. Thermal Transfer Labels
Understanding the specific applications for each type of label can help you determine which is best suited for your needs.
Ideal Uses for Direct Thermal Labels
Direct thermal labels are ideal for short-term applications where labels are not exposed to harsh conditions. Some common uses include:
- Shipping Labels: Quick and cost-effective for temporary use.
- Receipts: Efficient for high-volume printing in retail environments.
- Temporary Tags: Suitable for short-term identification needs, such as event passes or temporary badges.
Ideal Uses for Thermal Transfer Labels
Thermal transfer labels are best suited for applications requiring durable, long-lasting labels. Typical uses include:
- Product Labels: Perfect for labeling products that need to withstand handling and exposure to elements.
- Asset Tracking: Durable labels for tracking equipment and inventory over the long term.
- Laboratory Samples: Resistant to chemicals and moisture, ensuring label integrity in scientific environments.
- Outdoor Labels: Suitable for outdoor use where labels need to resist weather conditions.
How to Choose Between Direct Thermal and Thermal Transfer
Choosing the right label technology depends on several factors, including the intended use, environmental conditions, and budget constraints.
Key Factors to Consider
When deciding between direct thermal and thermal transfer labels, consider the following factors:
- Environmental Exposure: Determine the conditions the labels will face. Direct thermal labels are best for controlled environments, while thermal transfer labels are more suited to harsh conditions.
- Expected Lifespan: Consider how long the labels need to last. Direct thermal labels are suitable for short-term use, while thermal transfer labels offer longevity.
- Budget Constraints: Evaluate your budget for both initial setup and ongoing costs. Direct thermal labels are more cost-effective initially, but thermal transfer labels may provide better value in the long run.
Decision-Making Tips
Here are some practical tips to help you make the right choice:
- Assess Total Cost of Ownership: Consider both the initial investment and the ongoing costs of supplies and maintenance.
- Evaluate Physical Label Requirements: Think about the material, durability, and size of the labels you need.
- Match Label Type to Application: Choose direct thermal for short-term, high-volume applications and thermal transfer for long-term, durable labeling needs.
Making the Right Choice
Choosing the right label comes down to how you’re using it. Direct thermal labels are great for short-term jobs like shipping, while thermal transfer labels are built to last in tougher conditions.
No matter what you’re labeling, Label Blanks has the right thermal labels to keep your business moving. Shop our full selection today and find the best fit for your needs.
FAQs
What are the key differences between direct thermal and thermal transfer labels?
Direct thermal labels use heat-sensitive material and are best for short-term applications, while thermal transfer labels use a ribbon to produce durable, long-lasting prints suitable for harsh environments.
How do I decide which label type to use?
Consider factors like environmental exposure, required label lifespan, and budget. Direct thermal is cost-effective for short-term use, while thermal transfer is better for long-term durability.
Are thermal transfer labels worth the higher cost?
Thermal transfer labels are worth the investment if you need durable, long-lasting labels that can withstand harsh conditions. They are ideal for asset tracking, product labeling, and other applications where longevity is crucial.